- Thorlabs PF20-03-P01 Protected Silver Mirror
- Thorlabs PF20-03-P01 Protected Silver Mirror
- Light Source
- Plane Wave
- Circular, 5 mm radius
- 633 nm wavelength
- Power, 1 W
- Detector: Spot Analysis
- Spot: Coherent Irradiance
- Analysis Rays: 1 million
- 200×200 pixels
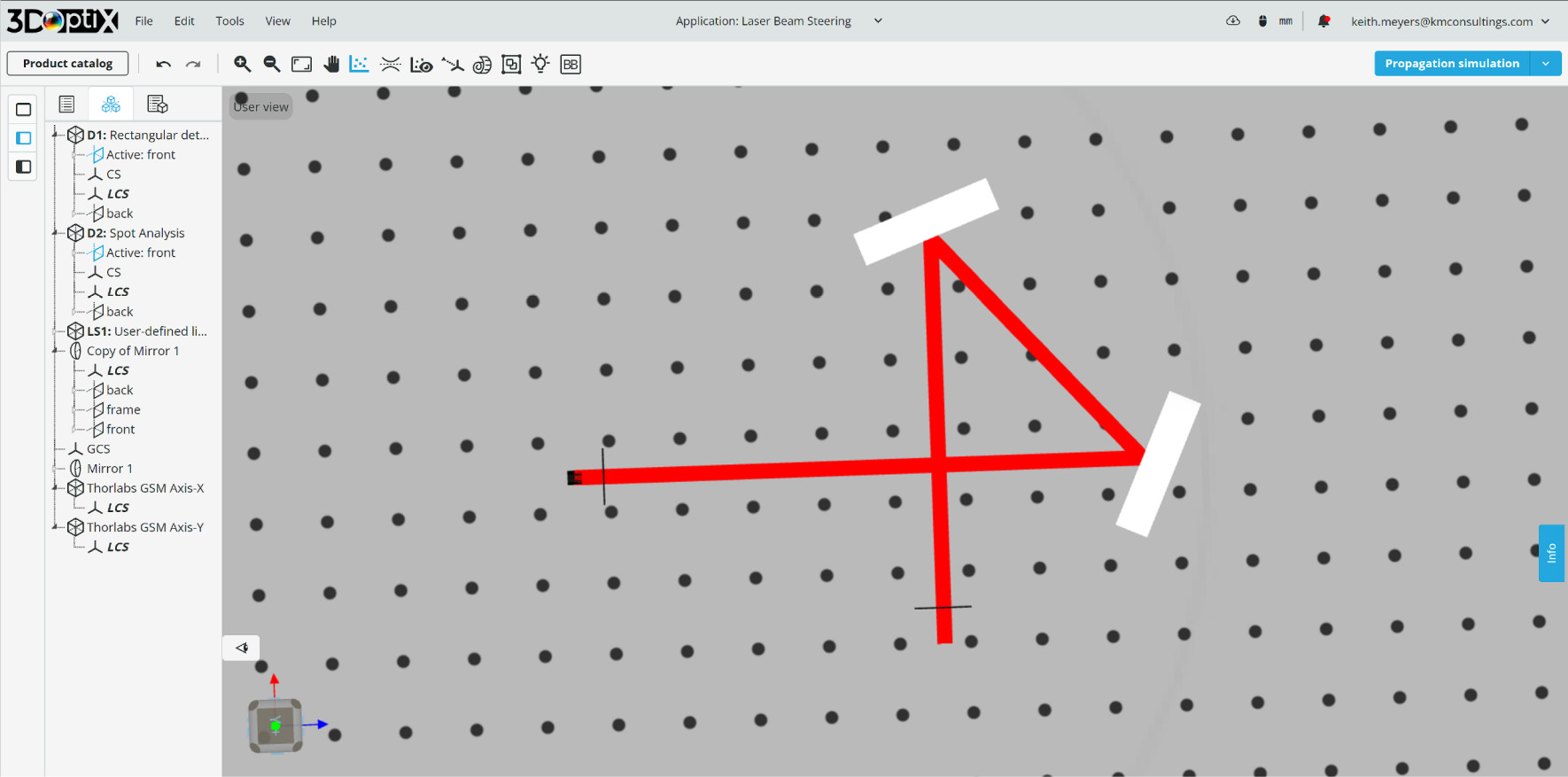
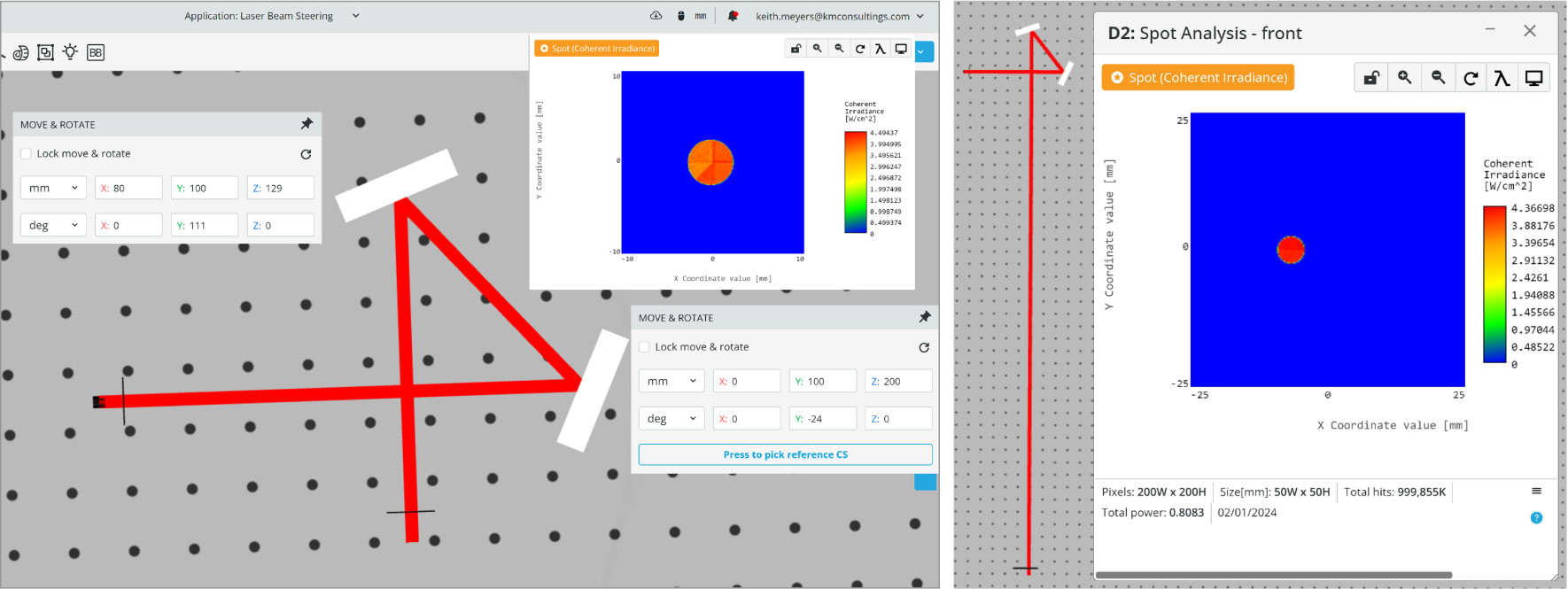
- Thorlabs GVS41, 1D Large Beam (10 mm) Diameter Galvo System
- Thorlabs GVS41, 1D Large Beam (10 mm) Diameter Galvo System
- Light Source
- Plane Wave
- Circular, 2 mm radius
- 633 nm wavelength
- Power, 1 W
- Detector: Spot Analysis
- Spot: Incoherent Irradiance
- Analysis Rays: 1 million
- 200×200 pixels
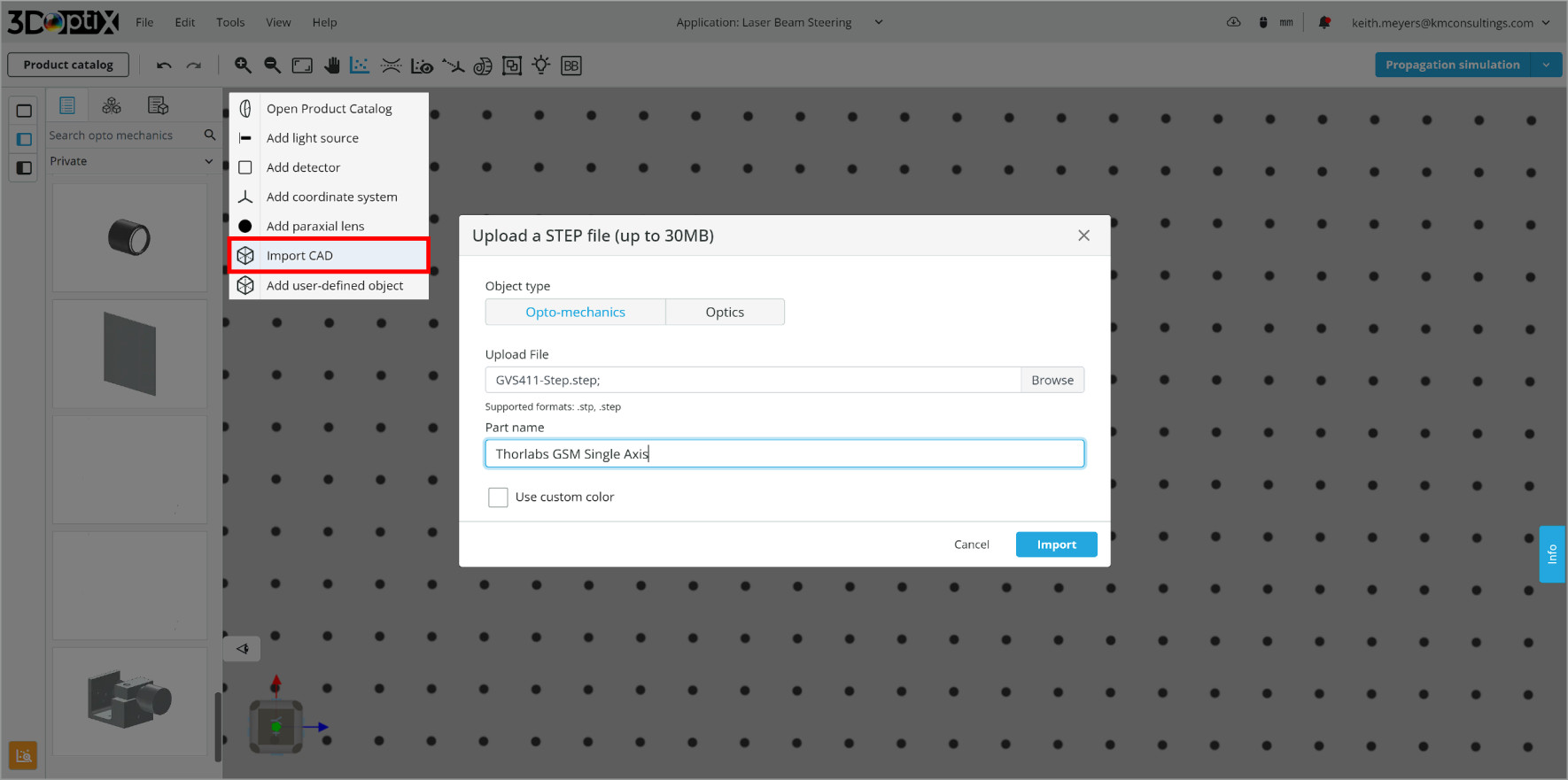
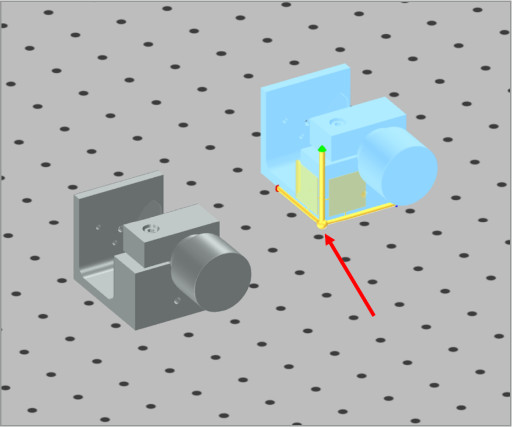
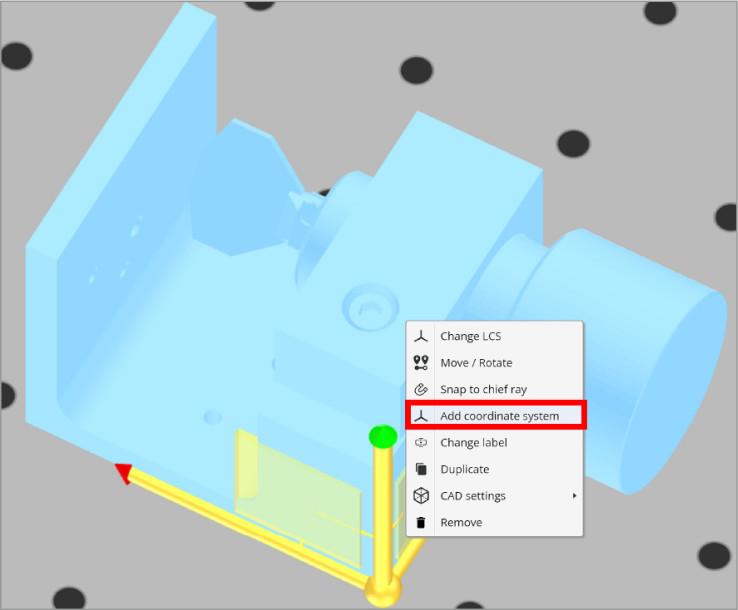
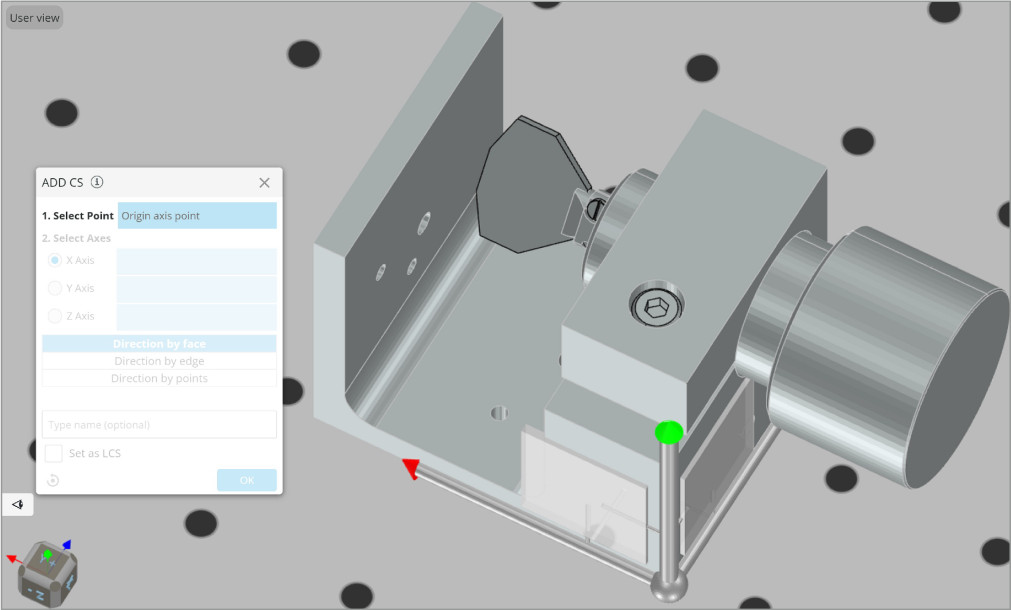
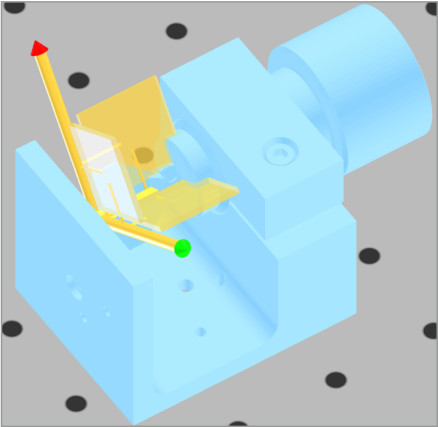
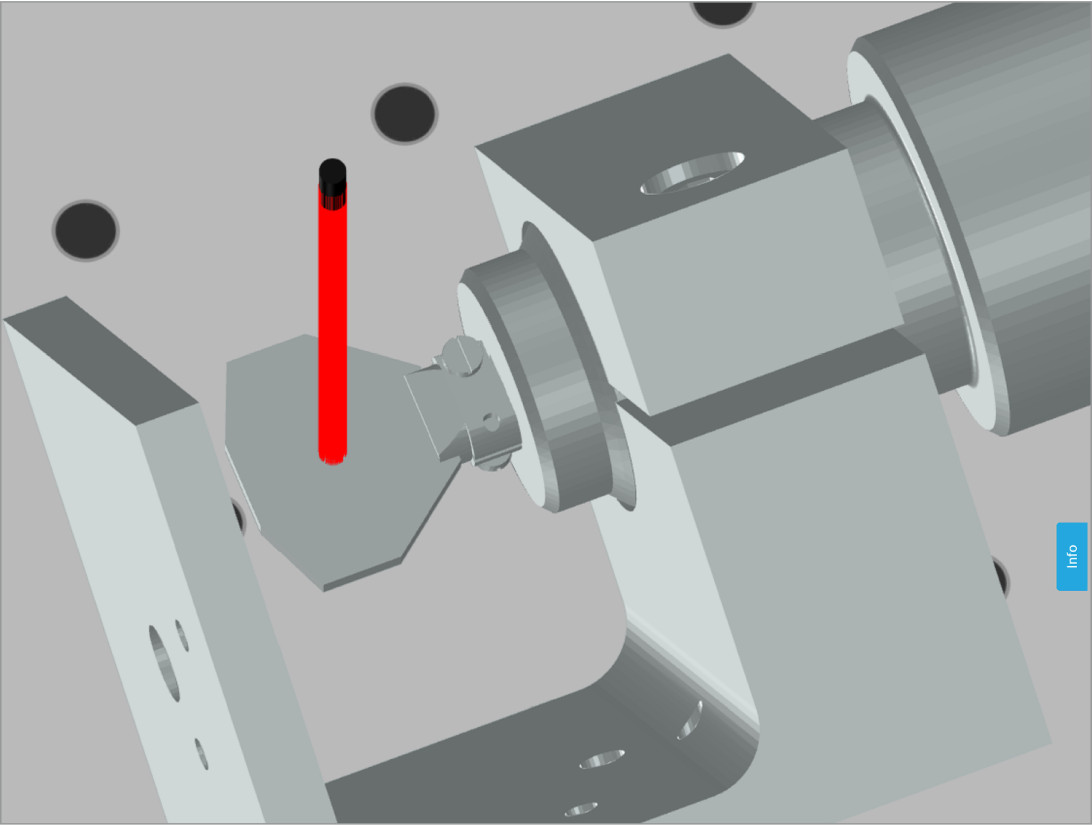
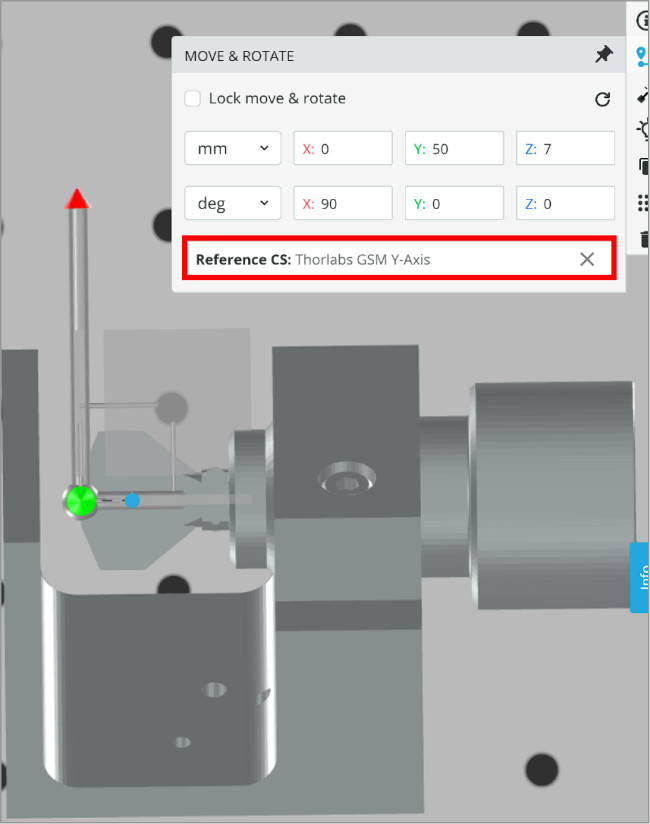
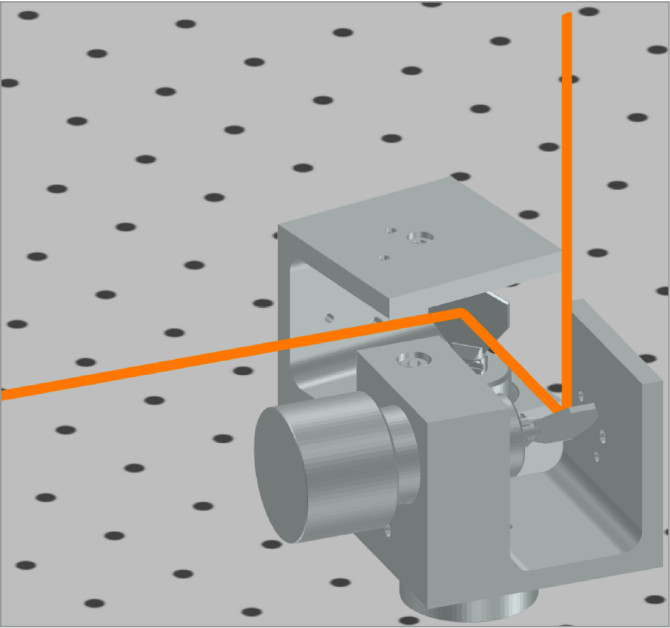
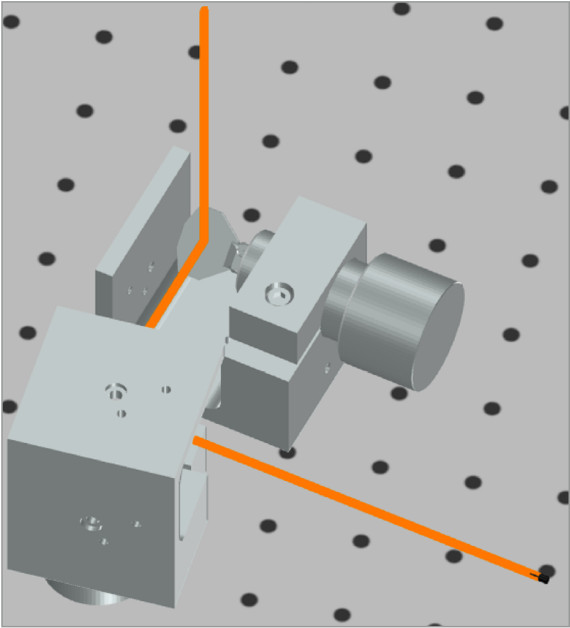
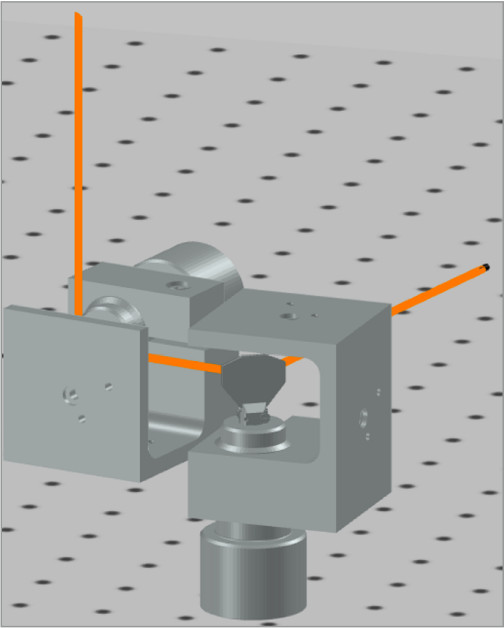
With the three objects aligned, we need to group them together using the GROUPING TOOL. This will prevent any unintentional misaligning and make it easier to reposition the system.
After grouping, the group can be moved in the 3D layout or using the MOVE/ROTATE ribbon button. This will make it simpler to rotate the system and direct the light output along another axis.
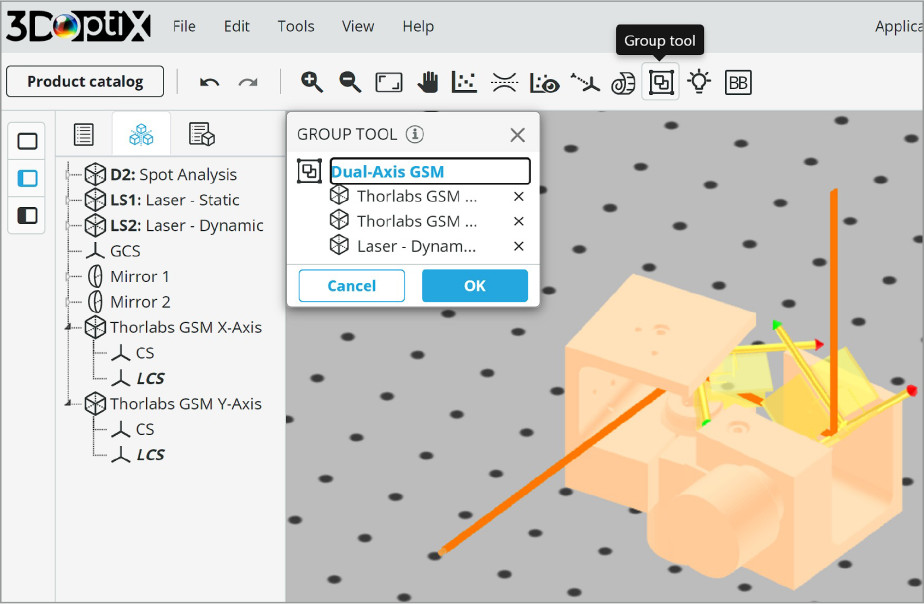
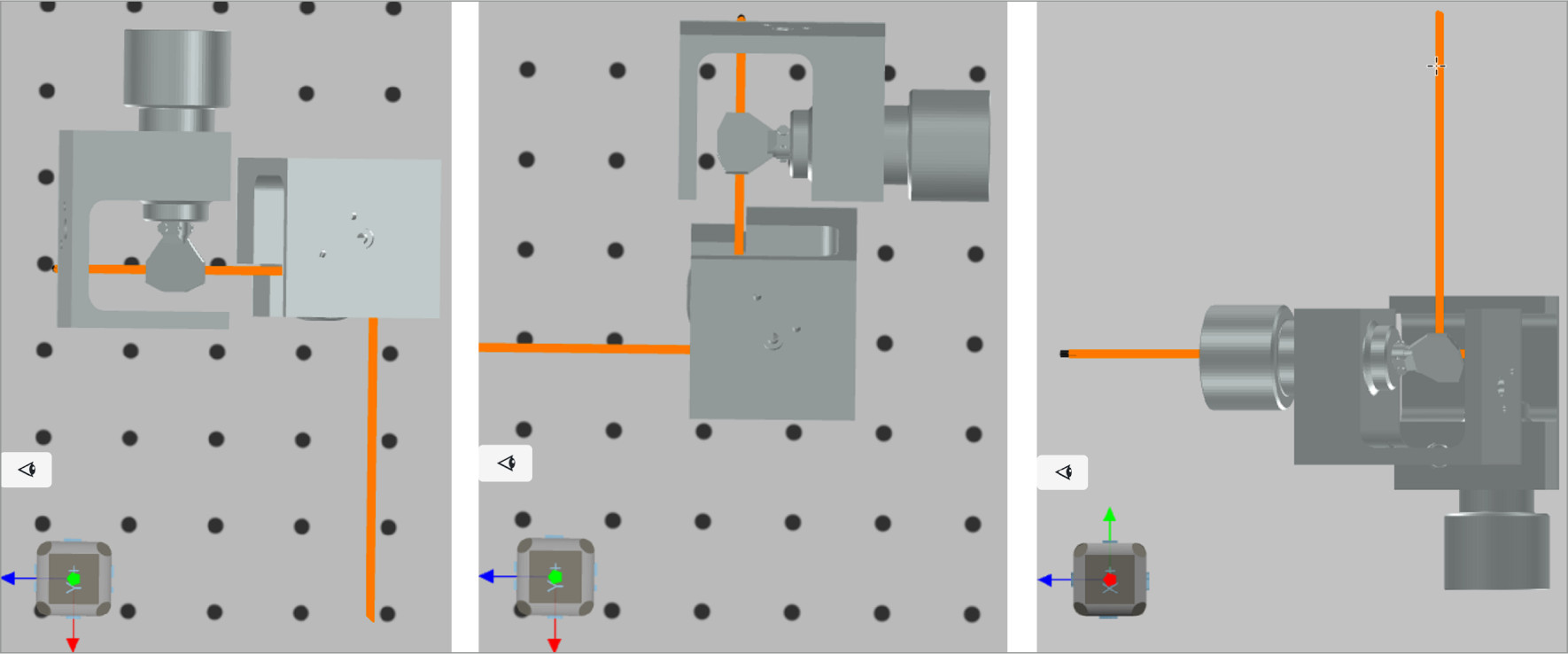
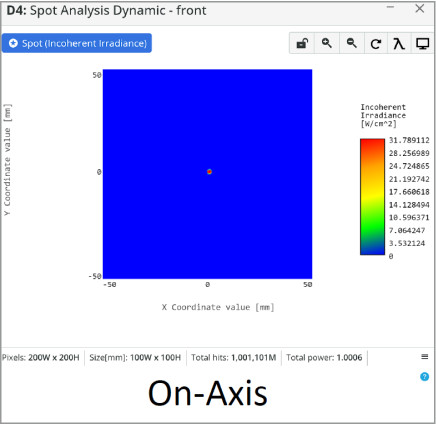
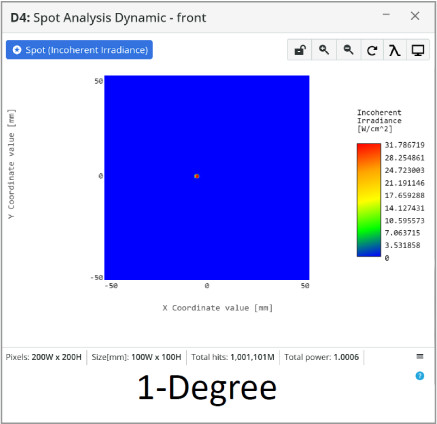

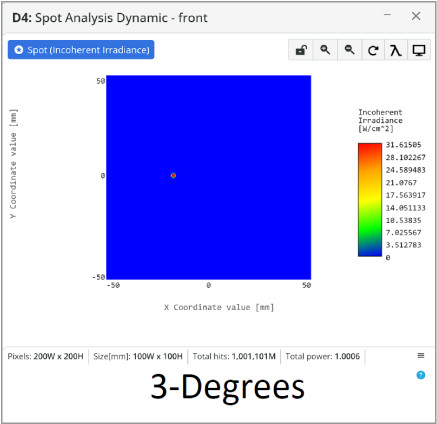
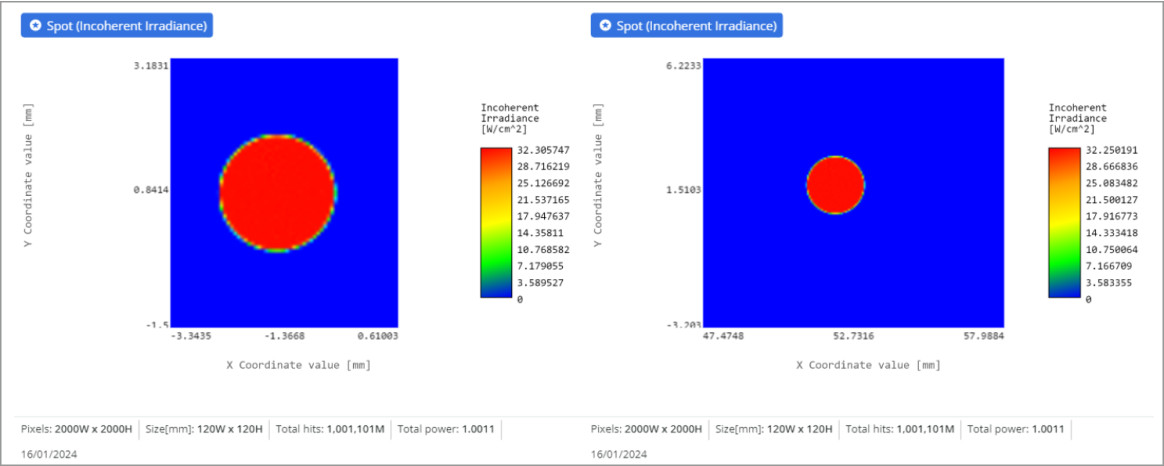
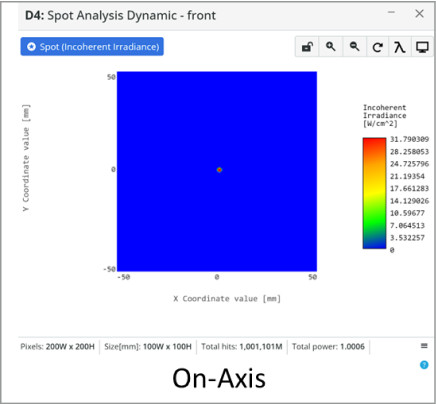
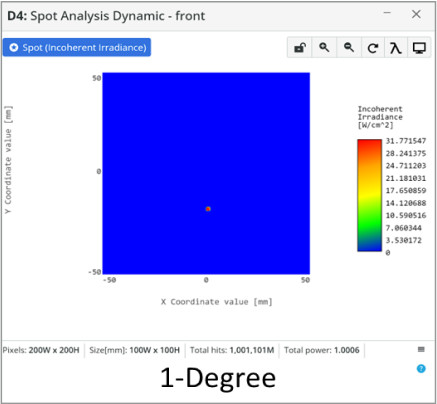
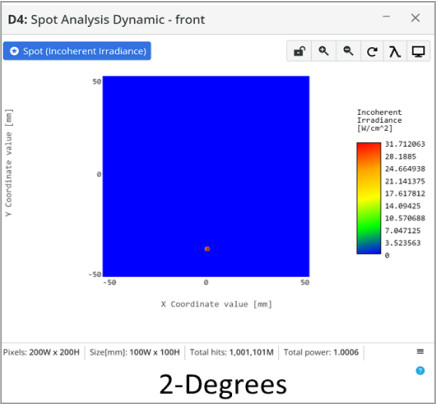
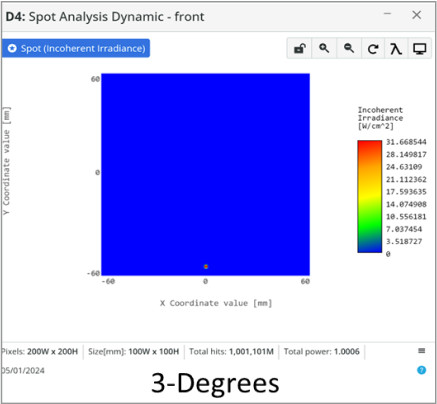
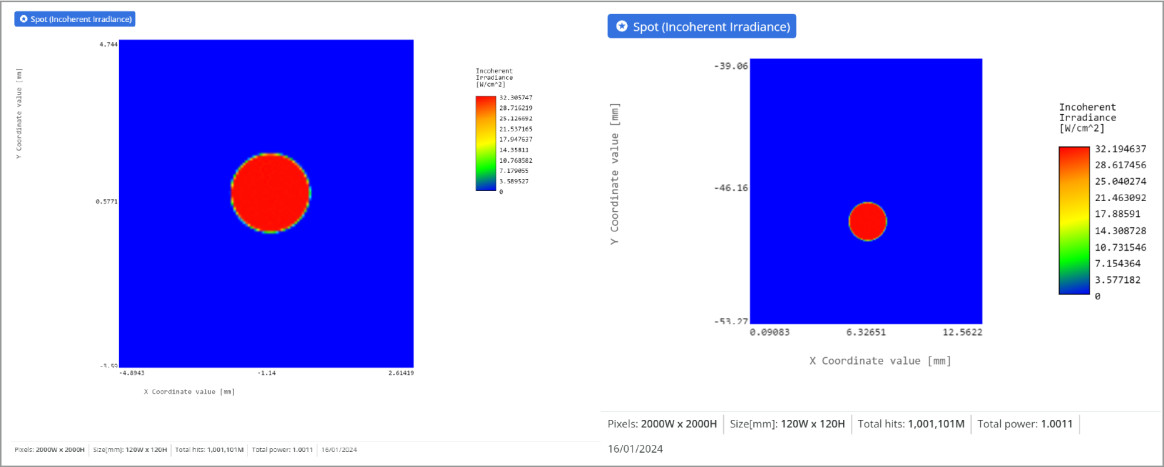
The last optical system will be a simple example of a more complex system. The F-Theta lens is a lens system that creates a flat focal plane tangent to the optical axis and creates a linear relationship between the angle out and the target plane position. This removes off-axis spot size variations over a certain input angle range and the need for algorithms to calculate the non-linear position on the target plane.
For a normal spherical lens, the focal plane is curved and the best spot size performance occurs on-axis when scanning a collimated beam. An F-Theta lens system creates a flat focal plane that generates the same spot-size performance over a range of input angles for the same collimated beam.
- Paraxial Lens, 25 mm FL
- Light Source
- Plane Wave
- Circular, 5 mm radius
- 633 nm wavelength
- Power, 1 W
- Detector: Spot Analysis
- Spot: Incoherent Irradiance
- Analysis Rays: 1 million
- 200×200 pixels
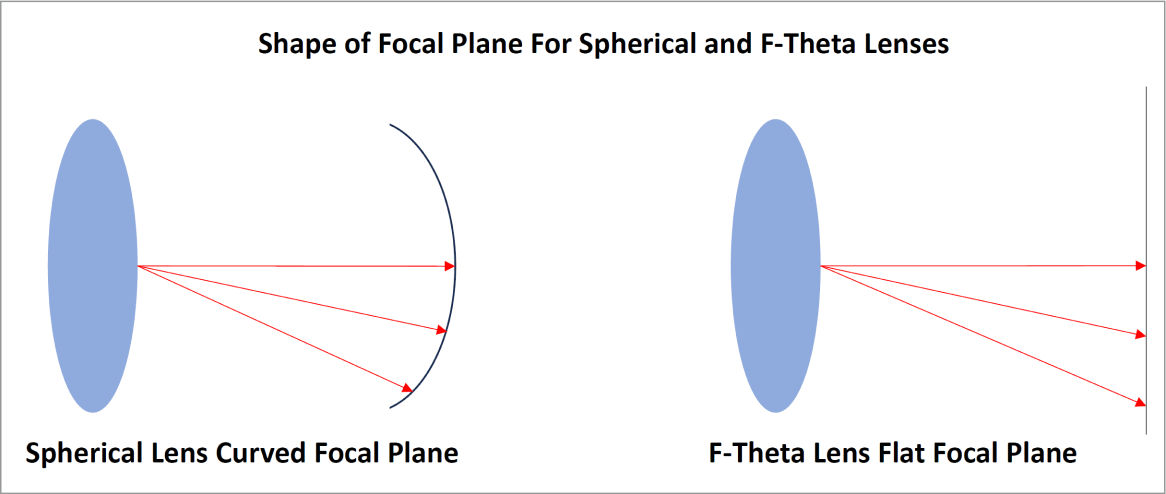
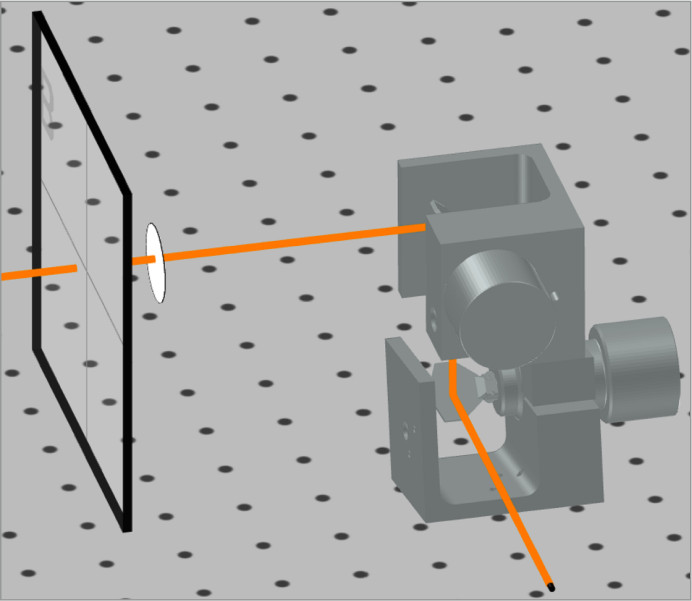
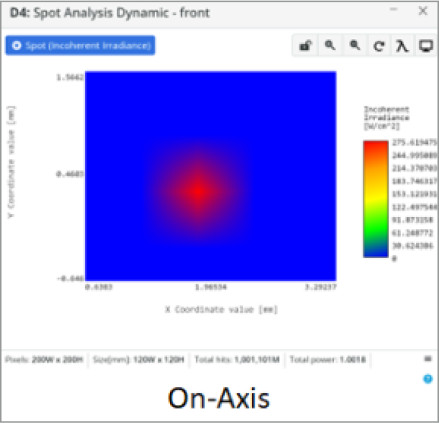
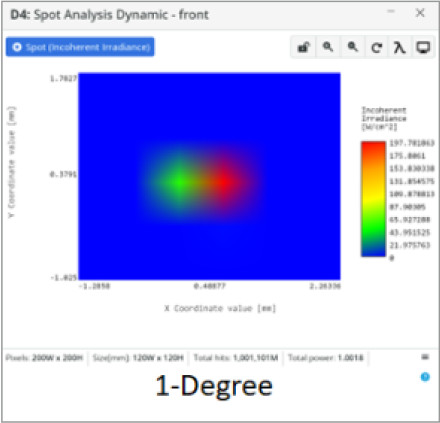
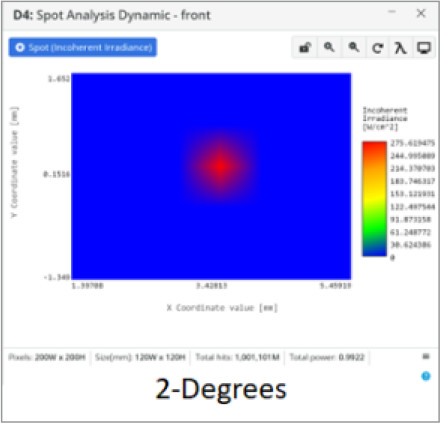
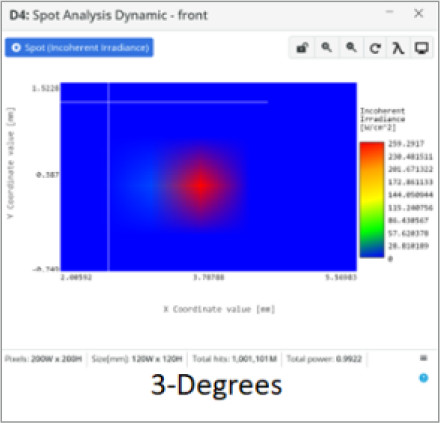
The paraxial lens scanned with the collimated laser beam using the dual-axis GSM provides a good example of this system but is not exact. The steering ability matched with spot size performance and positional linearity makes these very useful in applications where minimum spot size must be maintained over the scan angle, such as laser engraving. Similar to the dual-axis GSM the F-Theta input aperture diameter and focal length will be the limiting component for the steering extent.
The three laser beam steering systems overviewed have a variety of benefits, limitations, and design types. The specific system chosen will be a function of needed performance and laser output requirements for the application. Simulating laser beam steering systems to confirm or improve performance is a great method to create high-quality optical systems.