VIRTUAL LAB
Introduction to Optical Lens Properties
Approximately 3 hours (self-paced)
- Understand how optical substrates and surface curvature affect light
- Calculate the focal length of a lens using the thin and thick lens equations
- Use the Abbe number to understand the dispersion of a lens
- Conduct basic analysis on spherical aberration
- Incorporate best practices for using lenses in an optical system
Optical Substrates and Surface Curvature
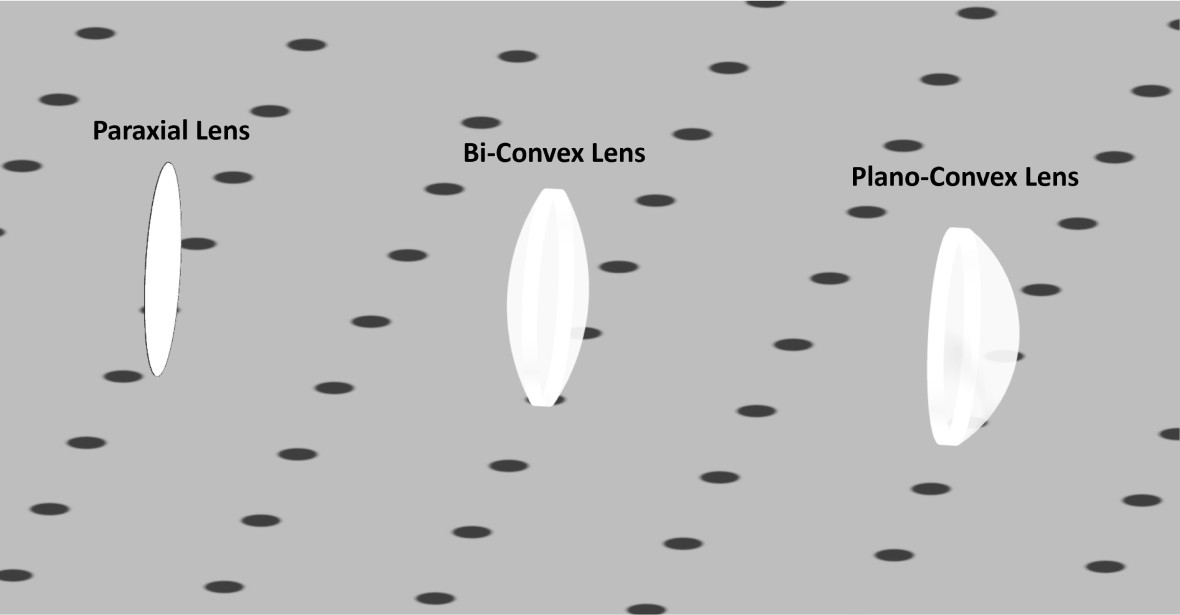
Focal Lengths of Various Lenses

- Using Equations 1, 2, and 3 from the previous section fill out the table below.
- Keep the simulation file open for the next exercise.
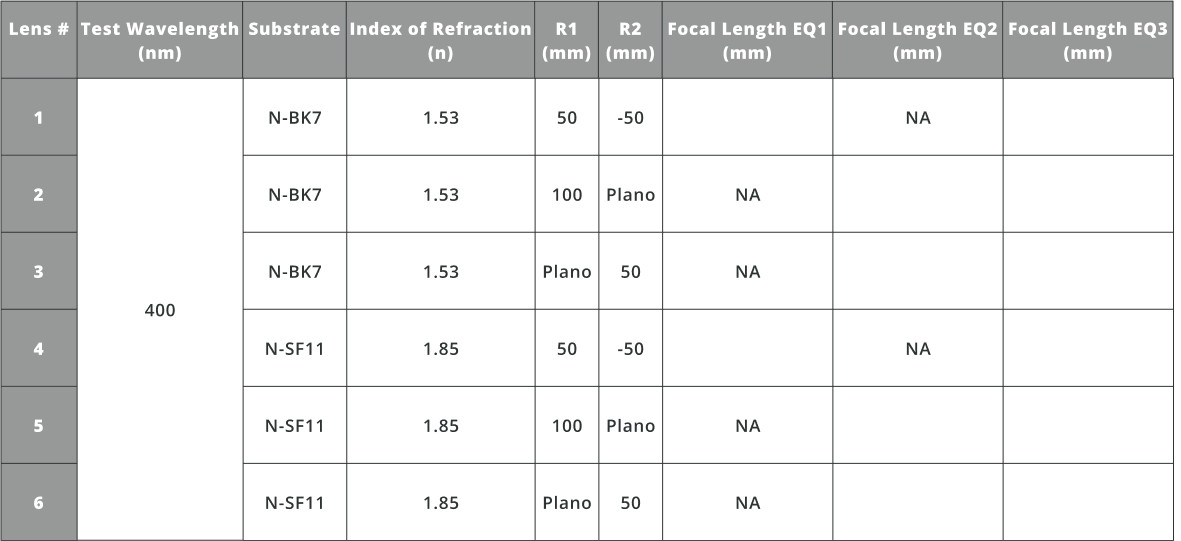

- Go to the menu bar at top and click tools, then select the lens calculator (see fig. 2).
- Fill out the table below using the values calculated in the lens calculator (see fig. 2).
- EFL, FFL, and BFL stand for effective, front, and back focal length.
- Compare the values from focal length calculations in Exercise 1.
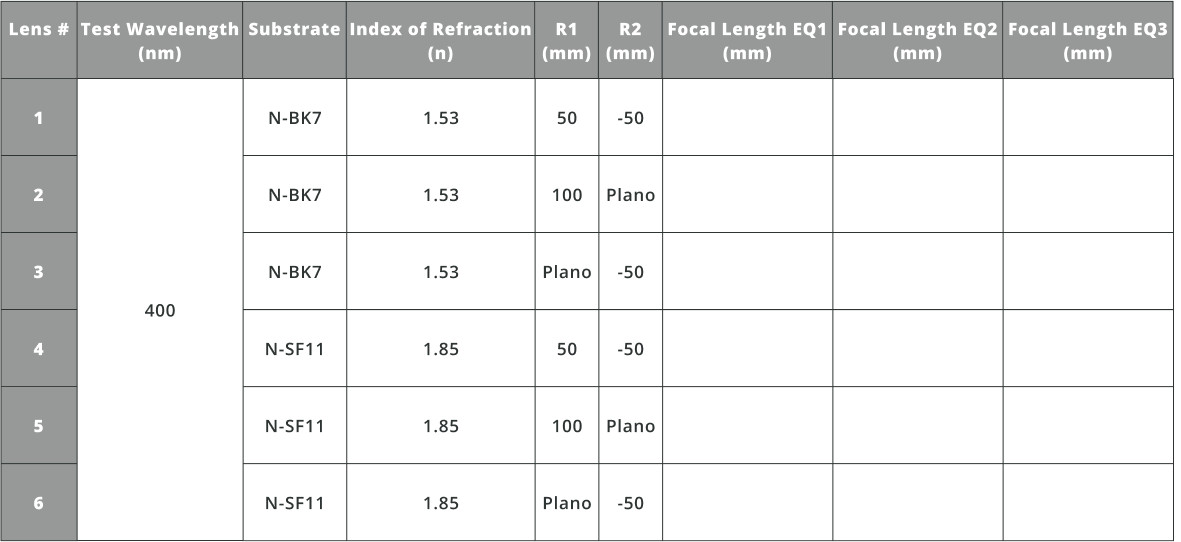
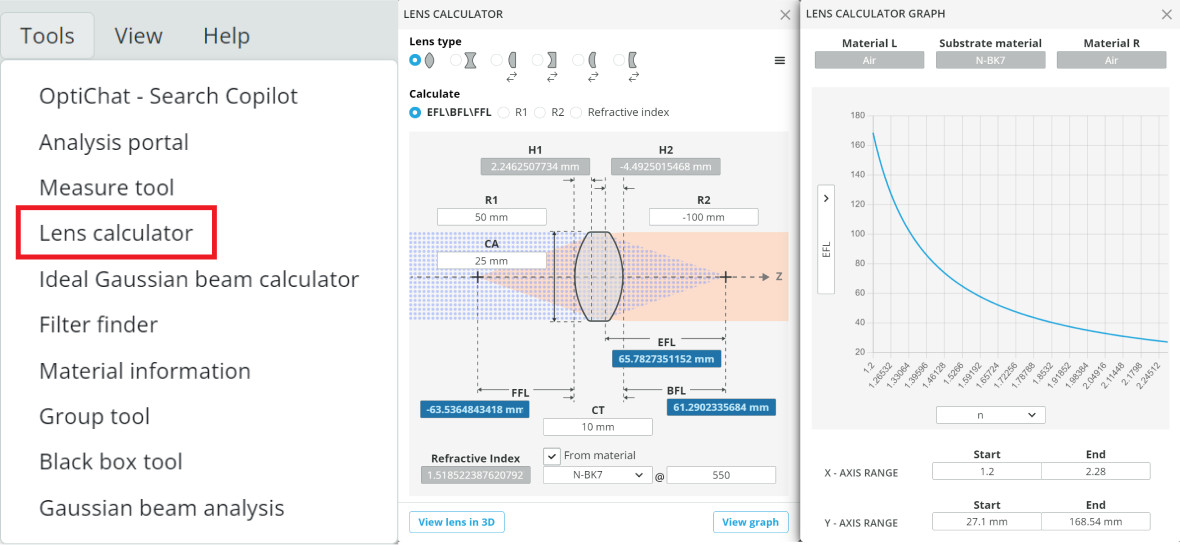
- Next, in the 3D layout right click and select add user-defined object.
On top of calculating lenses’ values, and adding and modifying lenses from the catalog, a lens can be created using this method.
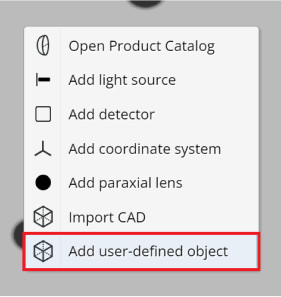
- Create lens #1 from Exercise 2 and add to the 3D layout by clicking save.
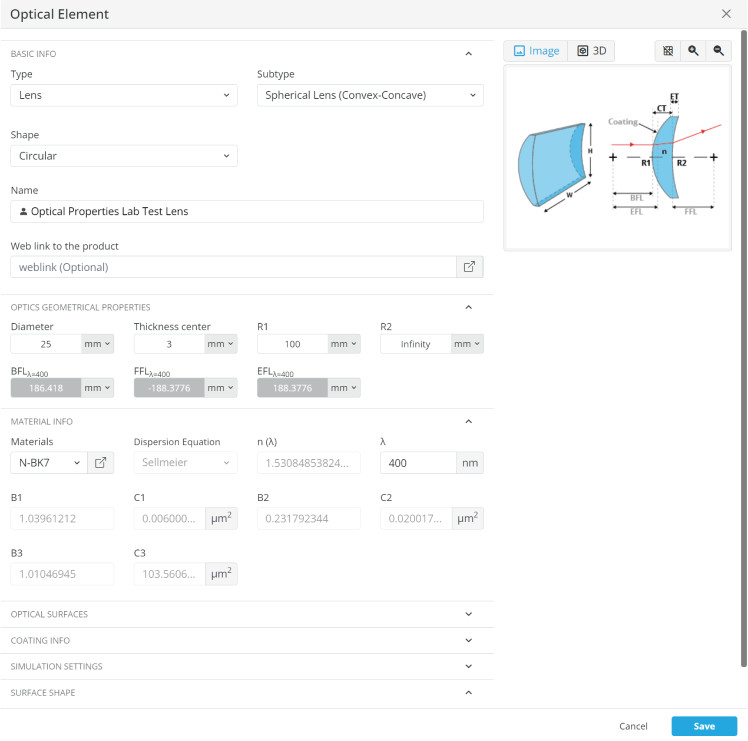
- Right click in the 3D layout and select Open Product Catalog.
- Find a lens using the filters on the left that matches the optical properties of the theoretical lens created using the add user-defined object method.
This is important for optical designers as ideal theoretical lenses are initially used to create an optical system, then readily available lenses are identified with matching properties for real prototype designs.
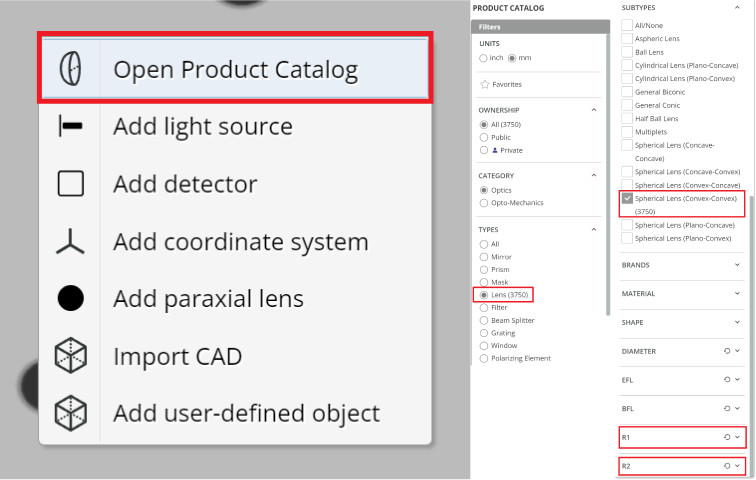
Abbe Number and Chromatic Aberration
The Abbe number, also known as the V-number, is a dimensionless number that characterizes the dispersion of a substrate. It is commonly used in optics to describe how much it disperses light into its component colors. The Abbe number is crucial in lens design, particularly in the correction of chromatic aberrations. This value is only used for optical glass transmissive in the visible spectrum as the calculations involved test visible test wavelengths. Generally, the range of values can be placed in the following two groupings.
- > 55, crown glass, indicates lower dispersion, less sensitivity to chromatic aberrations, more lens curvature needed
- < 50, flint glass, indicates higher dispersion, more sensitivity to chromatic aberrations, less lens curvature needed
There is an interactive diagram where the abbe number can be found on the Schott website for various optical glasses. Exploring the Abbe number means exploring the wavelength dependency of glass substrates. As the index of refraction changes over the transmissive wavelength range the bending of light rays will not be constant. This affects the manipulation of light and for imaging system the ability to focus light into a small spot.

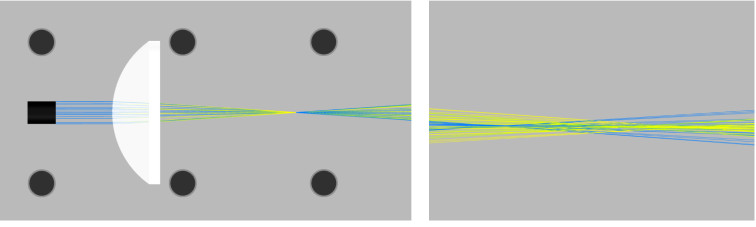

- In the 3DOptix app, import the file “Abbe_FL.opt“.
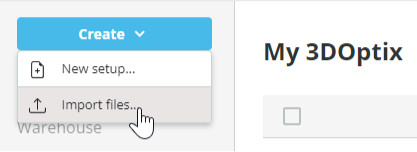
- Click on lens 1 and go to the optical settings.
- Change the wavelength under the material info tab to see the focal lengths for each respective wavelength.
- Enter the BFL values in the ideal BFL column.
Notice lens 1 front surface (curved) is facing the light source and the Plano surface (back) is facing the detector. Therefore, the BFL is needed for the distance from the detector measurement.
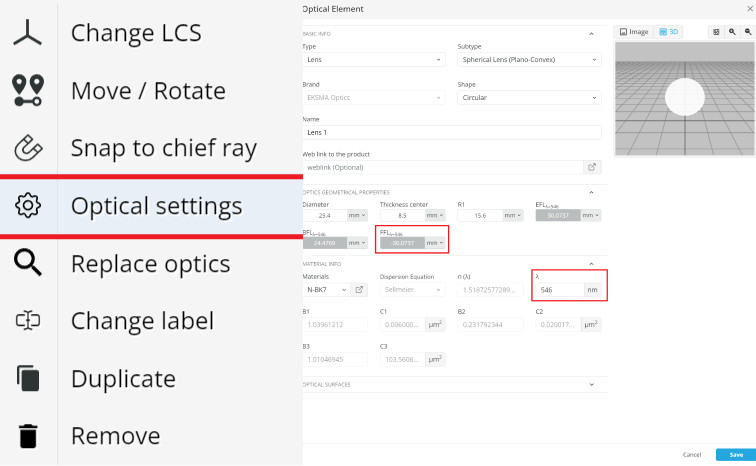
- Open the analysis window from the menu bar, change the detectors to advanced (Spot Incoherent), 300×300 X/Y pixels, and then run analysis.
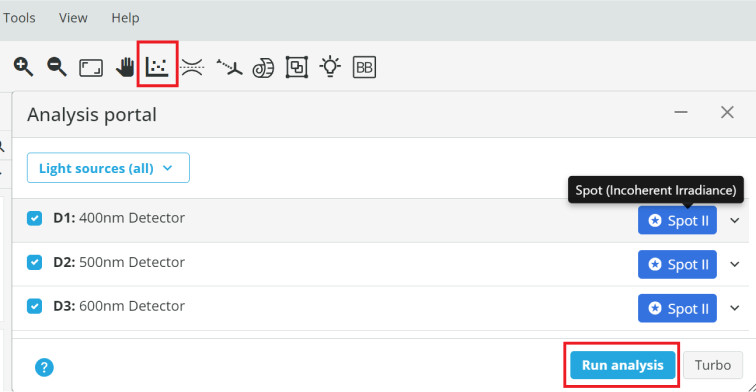
- View the detectors placed at the appropriate foci for the three wavelengths and measure the spot size using the measure mode tool and fit to circle.
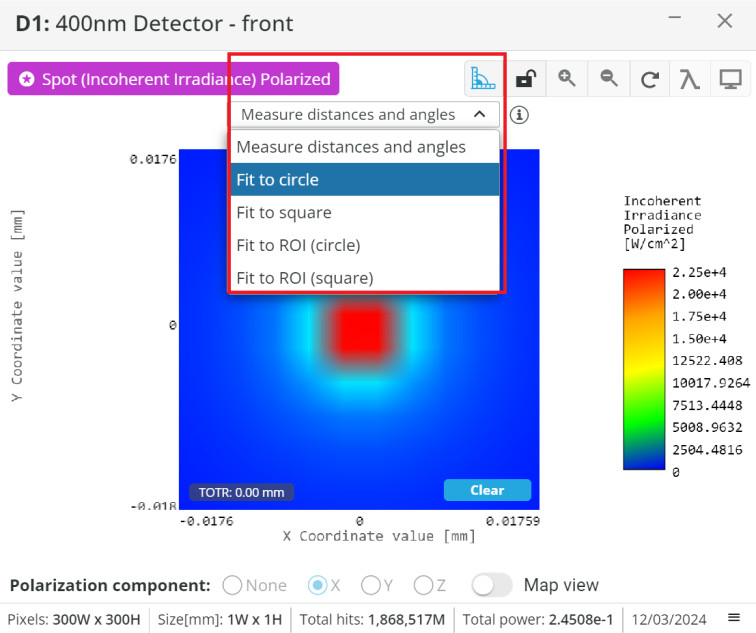
- Enter these values under ideal spot size
- Now place the three detectors at the ideal BFL of the 500nm test wavelength
- Enter this value under nominal BFL for each test wavelength
- Run the analysis again and measure the spot sizes
- Enter these values under nominal spot size
- Calculate the difference between the ideal and nominal BFL and spot size for all three test wavelengths
- The difference in spot size will show up in the final image as chromatic aberration creating rings of different colors
- Keep the simulation file open for the next exercise
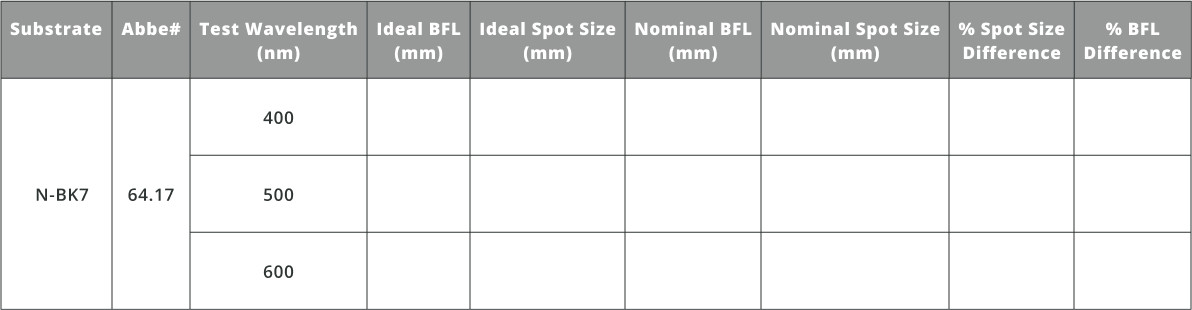

- This time replace the glass substrate with one having a lower Abbe number; N-SF11.
Notice the drastically lower Abbe number, which means higher dispersion.
- Complete the same analysis completed for N-BK7 lens above.
- Notice the difference in spot size compared to the N-BK7 lens.
This is an important part of chromatic aberration correction.
Understanding glass types and their wavelength specific optical properties leads to better designs.
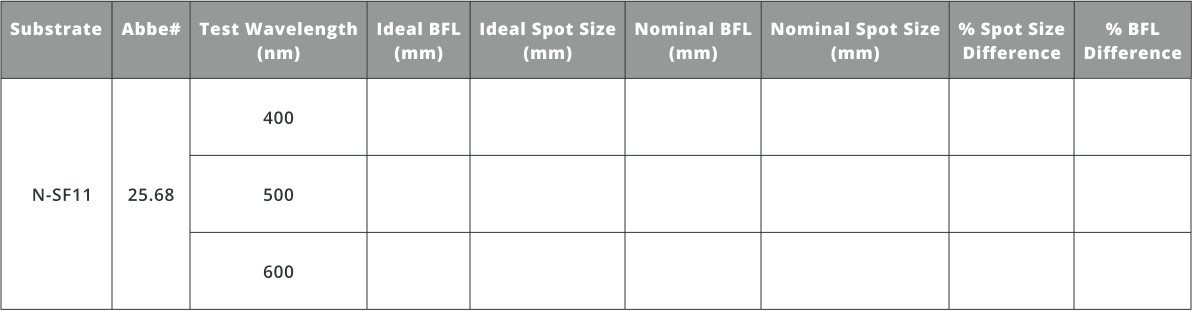
Spherical Surfaces and Spherical Aberration
Spherical aberration can be corrected using non-spherical surfaces such as parabolic and aspheric shapes. Analysis is done by tracing rays finding where the marginal and paraxial rays focus lies on the optical axis. There will be both longitudinal (LSA) and transversal (TSA) spherical aberration for any spherical lens. The LSA is measured from the marginal ray focus to the paraxial focus, and the TSA is measured from the paraxial focal plane to where the marginal rays intersect it transversally. The “circle of least confusion” is a plane parallel to the optical axis where the spot size is minimized. This location is given where the smallest spot size can be physically realized.
- Spherical aberration is proportional to the radial height a ray hits a lens to the fourth power: r4.
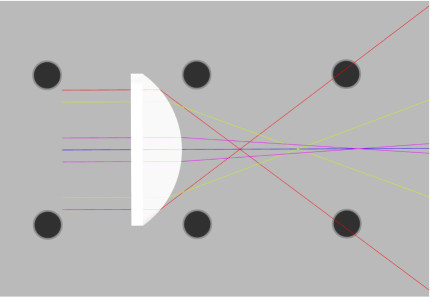
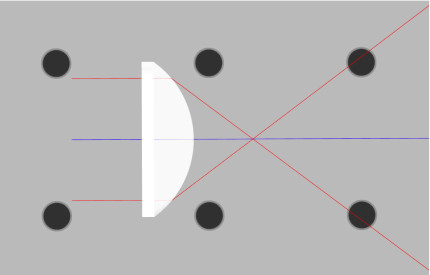
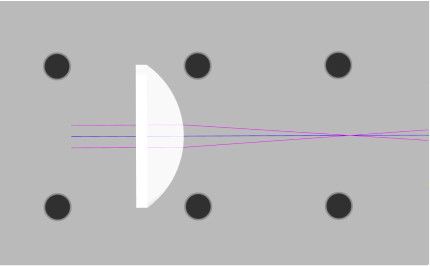
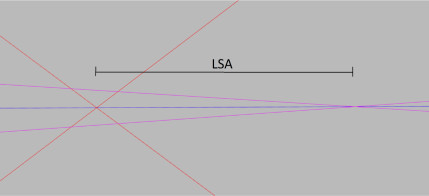
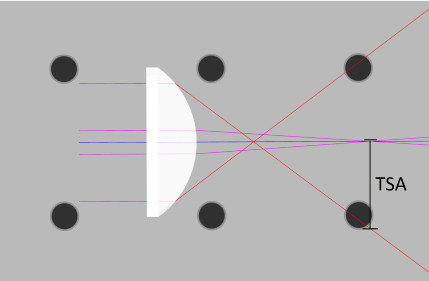
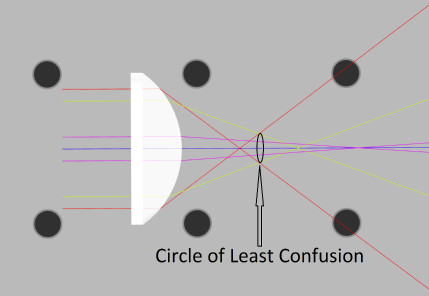

- In the 3DOptix app, import the file “Spherical_Abb.opt“
- Click on the lens and select optical settings, then change the wavelength to 400nm and record the FFL
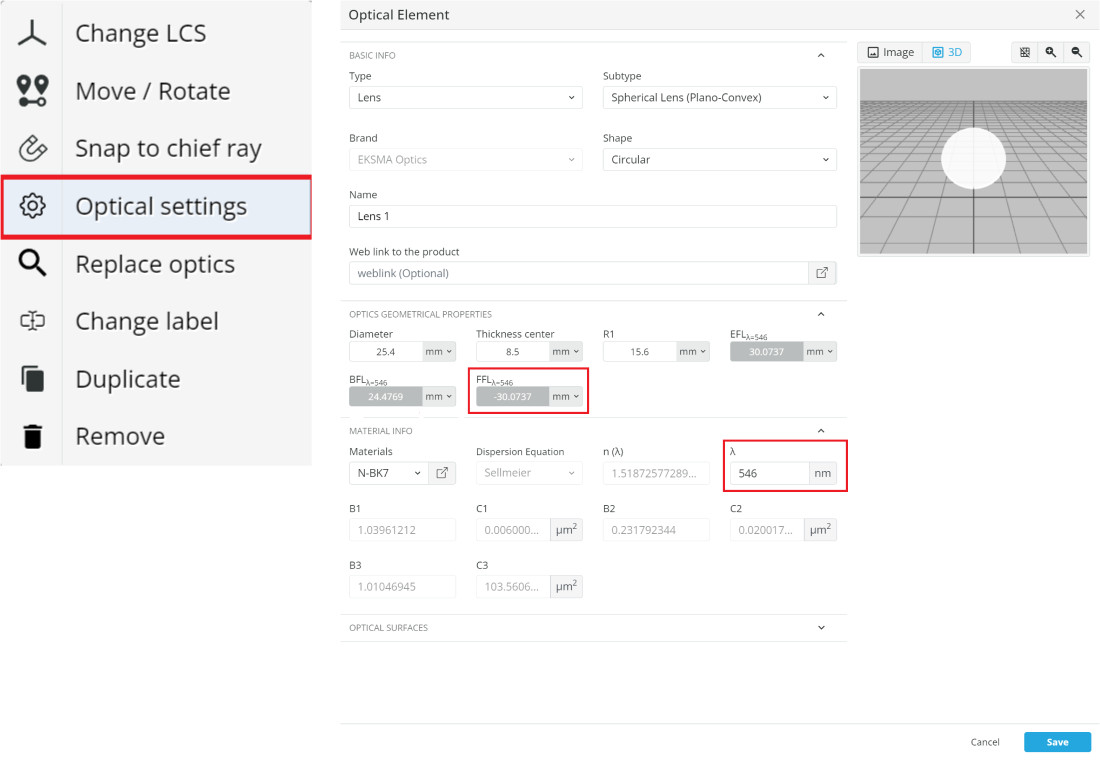
- At the upper right of the screen click the propagation simulation button.
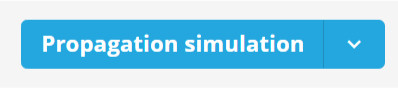
- There will be seven rays traced through the lens. There is one central ray and six symmetric about the optical axis of the lens simulating rays hitting the same location at the top and bottom. Measure the distance between the lens surface to the two foci in millimeters. See fig. 7.
- Take the foci for each ray pair and subtract these numbers; paraxial focus – marginal ray focus.
Positive LSA means the means that marginal rays intersect the optical axis in front of the paraxial focus, and negative if behind it.
- Measure the TSA by finding the transverse distance to where the marginal ray intersects the paraxial focal plane. See Fig 8.
- Find and measure the circle of least confusion where the marginal rays and paraxial rays meet to create the smallest spot size. See Fig. 9.
This is the point where the eye or camera should be placed for best imaging.
- Record the data in the table below.
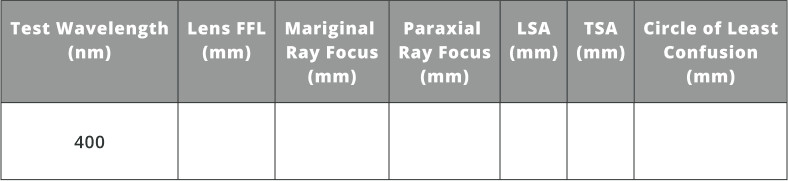
Methods to reduce spherical aberrations are reducing the ray heights when they enter a spherical lens, using non-spherical surfaces, and using equal amounts of positive and negative lenses. These techniques aim to enhance the overall performance of optical systems and achieve better image quality.
Optical Lenses Best Practices

- In the 3DOptix app, import the file “BP_Spherical.opt“.
- There are two plano-convex lenses in this file, one with the curved surface facing the light source and one facing the detector. There will be spherical aberration present for both and it is desired to determine the best orientation of the lens to reduce this.
- Repeat the procedure from Exercise 5 and fill in the table below
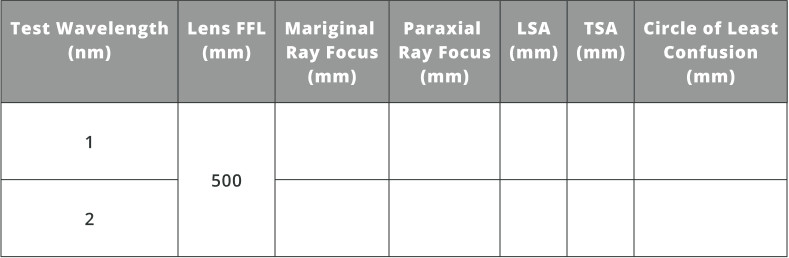

- In the 3DOptix app, import the file “BP_Collimate-Focus.opt“.
- There are two lens system configurations in the simulation file similar to Exercise 6. This time it is desired to determine the best orientation for the plano-convex lens to focus to a point.
- View the detectors placed at the appropriate foci and measure the spot size using the measure mode tool and fit to circle.
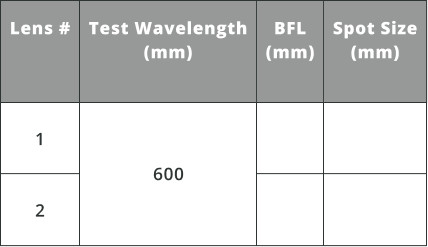